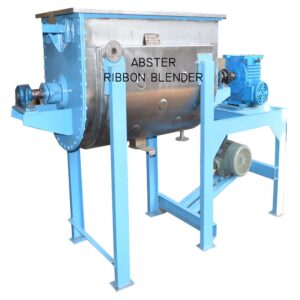
Ribbon type Mixer Principle of operation
Ribbon type Mixer are a specific type of powder blenders that consist of 2 parts mounted on a central shaft . The mixing medium often consists of inner and outer helical ribbons that are designed to move material both inwards and outwards. The external helical ribbons pull product from the sides of the mixer into the middle and the internal ribbons push the product back to the sides. The back-and-forth folding motion of the materials to be blended creates a convective mixing pattern.
The ribbons are designed to have precise gap tolerances between the walls of the mixer. In some instances, they can even be designed with soft material wipers to help keep product from building up on the sides. The drive mechanism often consists of a belt drive for the powder transmission between the motor and gear box. This arrangement would use a system of flexible belts and pulleys to produce the desired speed and torque required for the specific mixing application. However, more manufacturers are starting to use direct drives via gear motors that utilize a motors low inertia rotor to specifically match the gearbox unit. The advantage of this arrangement means less maintenance over the life of the industrial mixer.
Make sure to understand the required volume capacity of the mixer you are in need of. Knowing the bulk densities of the ingredients to be mixed is crucial to understanding the required capacity of your mixer, and more importantly the needed motor power required to mix your batches properly. Most standard design mixers will work just fine with a product bulk density of 35 lbs./ft³. However, once you start mixing denser batches the need for heavy duty motors and gear ratio changes will also be required.
2. Main benefits of ribbon blenders
Ribbon mixers are the most versatile and widely used type of powder blending machine in the market. They often are most commonly used for solids on solids mixing but can also be used for applications involving coating a dry particle with a liquid ingredient, or even particle absorption of a liquid addition. Rarer applications do allow for slurry and liquid particle suspension mixes with careful design and consideration to detail.
Because of the convective mixing pattern of the ribbon blender, short and fast mixing cycles are possible often ranging from a few minutes up to 20 minutes (depending on the volume and complexity of the formula). Considering the fast-mixing cycles of these bulk solids blenders you would think the ribbons run at a very high RPM, however this is not so. The ribbon agitators typically run no faster then 300 feet/min tip speed. This low speed creates a gentle folding action of the particles to be mixed. Therefore, this allows use on fragile and friable materials while preserving the particle integrity.
Ribbon mixers are also capable of full discharge via a centrally located discharge port. By running the mixer at low speed, product can be easily pushed back and forth until the mixing vessel is nearly empty. A variety of powder valves can be used on the discharge port of the mixer, but most common are plug valves. Plug valves offer the advantage of being flush with the internal surface of the mixer body when in the closed position, which prevents material build up during the mixing cycle. Working volume capacities of a ribbon mixer are often as low as 30% capacity, any less would not allow sufficient contact between the ribbons and the materials to be mixed. In some applications, the mixer can work at near 100% capacity but often times the optimal mixing capacity is around 50-70% volume.
Thanks to the versatility and gentle mixing action of ribbon blenders, they have a long material list of applications including spices, instant recipes, drink mixes, nutraceuticals, cosmetics, polymers and plastic compounds, fertilizers and ceramics to name a few. They can be used in any industry dealing with dry materials such as: food and beverage, pharmaceutical, chemical, minerals and energy.
3. Other considerations
One important thing to take into consideration when building a ribbon mixer for your process is utilizing a variable frequency drive. A VFD will allow for smoother start up and less wear and tear and drive mechanisms when initiating the mixing process under full load. Delta starters, or electronic soft starters, can also be integrated into the controls to accomplish the same task, however they are only for single speed drives.
Another thing to consider is the internal surface finish of the mixer body and agitators. If you are working with a fairly free flowing mixed batch, then your standard 80 grit bead blast finish will do just fine. But for sanitary applications, or materials that tend to build up and stick to surfaces, 150 grit finishes may be more in order. Even mirror polished might be necessary to help facilitate the cleaning of the equipment and avoid cross contamination between batches. To further assist in avoiding cross contamination, your supplier should be able to design a mixer with an easily removable agitator for cleaning out of place and allow better access to the internal body of the mixer itself.
For batch mixes dealing with abrasive materials, such as ceramic powders, a Hardox liner can be applied to internal surfaces for better wear resistance. Other options to consider integrating are sampling devices to take real time samples during mixing, heating / cooling jackets to control the temperatures of the mix, and nitrogren purges to inert combustible materials.
In order to decide which powder mixer is best for your process, contact one of our experts. Palamatic Process has 30 years of powder handling experience and together, we can present your production line with a solution that will exceed expectations!