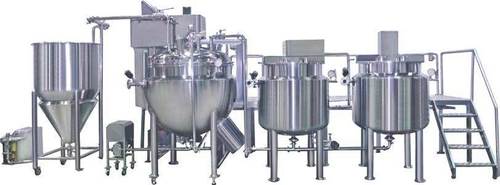
Ointment Manufacturing Plant
Cream Manufacturing Plants are high end systems uses modern technique to enhance production performance. Equipment comes handy in the production of quality products in industries such as pharmaceutical, herbal and cosmetic. Plant offers flexibility to producers and equipped with high class features which given it ten out of ten.
Abster equipment is excellent ointment manufacturing plant manufacturer in India with installations across the globe. Our plants are cGMP certified and having validation protocols for regulatory requirements. It has PLC system with touch screen MMI and SCADA packages optionally. As you have variety of packages at your disposal, so you do not need to look elsewhere for cream, gel and toothpaste manufacturing plants.
Features of Ointment Manufacturing Plant
-
cGMP production plants.
-
Minimum human involvement needed.
-
Option of PLC, HMI based model.
-
21 CFR Part 11 compliant SCADA package available on demand. (optionally)
-
Almost zero vacuum drop during the mixing and blending process.
-
Uniquely designed to address all crucial factors directly or indirectly affecting the production quality.
-
Ideal for the production of variegated ointments, lotions, gels, emulsions. toothpastes and homogenizations.
-
All contact parts made of SS316 and teflon material.
-
Hydraulic lid lifting and tilting arrangement of the main vessel to facilitate cleaning at the time of product change over.
-
Specially designed stirrer with flexible teflon scraper.
-
Mixing principles are matching with international standards.
-
Variable speed provided for stirrer and homogenizer for different speeds.
-
All transfer done through vacuum to avoid any hand touch and contamination.
-
Homogenizer fitted in the main shaft to ensure high shear emulsification and homogenization of the product.
-
Specially designed inline filter to ensure proper filtration.
-
Minimum change over time.
-
Pneumatic / hydraulic lifting to lid manufacturing vessel
-
Mixing vessel consist of two speed agitators and one variable fast speed agitator.
-
The plant is designed to be operated by only one operator and one helper.
-
All vessels are cGMP.
-
Gaskets used are made of silicon materials.
-
The entire plant is equipped with CIP & SIP connections, so that customer can use this facility, if have CIP & SIP equipment.
-
All values of the temperature and time of the plant are indicated digitally on the control panel.
A standard semi-solid emulsion like ointment manufacturing takes place in three different phase vessels – A water phase vessel, wax phase vessel and a main mixing vessel. Other components may include an emulsifier/homogenizer, a vacuum pump, Transfer pump, storage and buffer vessels and a CIP module. All our vessels are made of SS316L grade material and fabricated as per cGMP guidelines. The plant can be completely automated with pneumatically operated valves for aseptic manufacturing.
Water phase vessel
All the aqueous phase mixing of ingredients is carried out in the water phase vessel with water or similar material as the solvent. The vessel could be jacketed for heating and cooling of the solution in the vessel. The temperature variation of the vessel could be achieved by steam & chilled water or electrical heating arrangement according to the availability of utilities at the customer’s facility. For uniform mixing, a propeller type stirrer is utilized along with baffles to prevent vortex formation. Product inlet into the vessel can be achieved via vacuum suction for minimum contamination. Similarly, solid ingredients can also be introduced into the solution at vacuum pressure. Solid ingredients can be introduced into the vessel via an additive hopper at the top of the vessel or a suction port situated at the bottom of the vessel. After obtaining the satisfied composition the contents of the vessel are transferred to the main manufacturing vessel.
Wax phase vessel
Similar to the water phase vessel, all oil/wax phase mixing is carried out in the wax phase vessel with wax as the main solvent. The vessel is usually jacketed for heating of the wax to improve solubility at elevated temperatures. The temperature variation of the vessel could be achieved by steam & chilled water or electrical heating arrangement according to the availability of utilities at the customers facility. For uniform mixing, a saw-tooth cutter type stirrer is utilized in this phase vessel. Product inlet into the vessel can be achieved via vacuum suction for minimum contamination. Similarly, solid ingredients can also be introduced into the solution at vacuum pressure. After obtaining the satisfied composition the contents of the vessel are transferred to the main manufacturing vessel.
Main Manufacturing vessel
The main mixing of the contents in the water phase vessel and the wax phase vessel is done in the main manufacturing vessel at appropriate temperature. The temperature variation of the vessel could be achieved by steam & chilled water or electrical heating arrangement according to the availability of utilities at the customers facility. Usually, the main mixing vessel is provided with a top mounted anchor type agitator to stir the product for uniform temperature transfer and minimizing lump formation. The agitator is also equipped with teflon scrapers for scraping of material from the walls of the vessels. Apart from the agitator, a homogenizer is provided at the bottom of the vessel for emulsification of the liquid-liquid mixture to a uniform composition. Propack technologies’ homogenizer is designed to reduce particle size to less than 5 microns. After attaining the desired composition and viscosity of the product, the contents are transferred into a storage vessel through a flush bottom diaphragm valve to minimize product holdup in the tank.
The operations of various pumps, pneumatically operated valves (in case of automated operation) and mixers is carried out through the main control panel. The panel is made out of SS304 grade material and consists of various safety lock systems like the Emergency stop and Mains supply indicators for safe work and extended component life. The vessels are connected to each other via interconnecting pipelines manufactured as per cGMP norms and connected with sealed tri clamp connection.
Features of our system:
- Uniform ingredient dispersion
- No wall caking
- Entire plant operation by one operator and one helper
- Efficient heat transfer in the vessels
- Particle size reduction less than 5 microns
- Reduced batch processing time
- Reduced change over time
- Consistent product composition across different batches