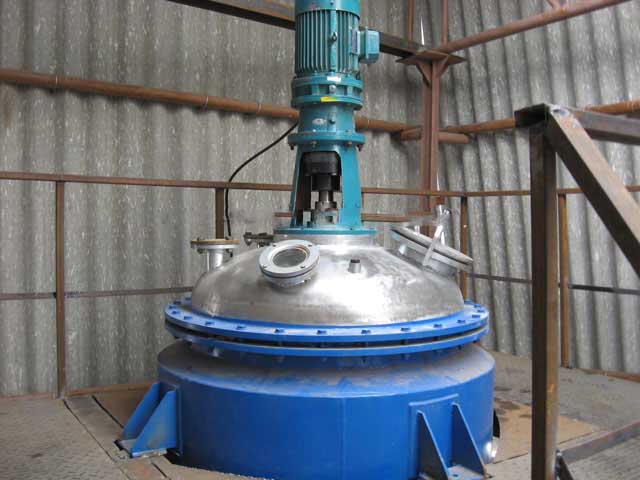
Polymerization/Photochemical/Phenol Continuous Stirred Tank Electric Heating Batch Chemical Stainless Steel Reactor Price
Mixer Type: | Agitator |
---|---|
Stirring Type: | Diving |
Application: | Liquid |
Certification: | CE, ISO |
Application Area: | Chemical |
Layout Type: | Verticle |
Polymerization Reactor Description
We will offer you price referring to your detail request, so please kindly inform us of the material, viscosity, density, etc, and
other requirements you prefer, and the special offer will be given.
The pictures are above just for your reference.
Our machines can be customized, leave an inquiry to know more details about price, packing, shipping and price.Any questions, feel free to contact us.
Polymerization/Photochemical/Phenol Continuous Stirred Tank Electric Heating Batch Chemical Stainless Steel Reactor Price |
Polymerization reactor is a new type of reaction equipment developed on the basis of absorbing domestic and foreign advanced technology. It has the characteristics of rapid heating, high temperature resistance, corrosion resistance, hygienic, no environmental pollution, no need for automatic heating of boiler, easy to use and so on. Used in petroleum, chemical, rubber, pesticide, dyes, medicine, food, used to complete the curing, nitrification, hydrogenation, alkylation, polymerization, condensation and other process
A chemical reaction takes place within an enclosed volume called a chemical reactor. The reaction occurs in the process vessel, which is usually a closed system. In chemical process analysis, a chemical reactant is an example of a chemical reactor. This unit operation is used to carry out a particular type of chemical reaction. Here, the concentration of a given reagent is controlled. Once the reagent has been added, it can be removed or mixed with other chemicals, as desired.
Depending on the type of reaction being performed, a chemical reactor may be classified as either a batch or continuous system. A batch reactor is ideal for low-scale production and is a great choice for multiple products or complex chemistry. It also provides important quality control. The process streams that are incorporated into the reactor are known as integrated circuits, and the duration of the integration is governed by the required concentration or conversion. In some cases, several types of continuous systems are used in an industrial process.
Polymerization Reactor Application
*Application of Resin plant:
Chemical Machine Resin Plant is the key equipment for producing all kinds of resins, such as Alkyd resin, Acrylic resin, PET resin, epoxy resins, ABS resins, Polyester resin, Unsaturated polyester resin, , Amino resin, curing agent.
The whole set of equipment includes reactor, vertical fractionating column, horizontal condenser, water storage tank, oil spill tank and piping (dilution kettle). All parts of the equipment that contact with the material are all made by stainless steel.
*Model selection reference of resin production equipment
Composition | Instructions |
Main Reactor | The size, material, heat transfer systems, mixing systems, sealing systems of reactor according to client’s specification |
Dosing Vessel | According to the client’s demand, it adopts gravity tank, gravity mixing tank, gravity dispersing tank, gravity emulsifying tank. |
Distillation Device | Vertical condenser, horizontal condenser and separator. |
Vacuum system | All kinds of vacuum pumps, buffer tanks. |
Thinning Vessel | The size, material, heat transfer systems, mixing systems, sealing systems of thinning vessel according to client’s specification |
Pipeline system | According to the client’s demand, it decides the heating, cooling, vacuum and material pipelines, and including related valves, flowmeters and expanders etc. |
Control System | According to client’s demand, it decides manual, semi-automatic or full-automatic system. |
Filter System | Frame filter, bag filter or centrifuge etc. |
Operation Platform | Steel platform or concrete platform |

Type Item |
500L | 1000L | 1500L | 2000L | 3000L | 5000L | 8000L | 10000L | 15000L | 20000L | 25000L | 30000L | 35000L |
Cylinder Size mm | 900×800 | 1100×1200 | 1300×1200 | 1400×15300 | 1600×1500 | 1800×2000 | 2100×22000 | 2200×2500 | 2600×2800 | 2800×3000 | 3000×3400 | 3200×3500 | 3200×4000 |
Actual Capacity L | 699 | 1400 | 2166 | 3000 | 4066 | 6600 | 10038 | 12300 | 19456 | 24205 | 31084 | 36706 | 40725 |
Outer Tube Size mm | Φ76/2 | Φ76/2 | Φ76/2 | Φ76/2 | Φ89/2 | Φ89/2 | Φ89/2 | Φ89/2 | Φ89/2 | Φ89/2 | Φ89/2 | Φ89/2 | Φ89/2 |
Heating Area m2 | 1.7 | 2.6 | 3.8 | 4.5 | 5.8 | 7.5 | 11 | 13.2 | 18.6 | 21 | 26 | 30 | 33 |
Inner Coil Size mm | Φ38 | Φ45 | Φ45 | Φ45 | Φ45 | Φ57 | Φ57 | Φ57 | Φ57 | Φ57 | Φ57 | Φ57 | Φ57 |
Cooling Area m2 | 1.6 | 2.7 | 3.6 | 4.3 | 5.7 | 8 | 11 | 13 | 18 | 21 | 25 | 30 | 33 |
Motor Power kw | 3 | 4 | 5.5 | 5.5 | 7.5 | 11 | 15 | 18.5 | 22 | 30 | 37 | 45 | 55 |
Pros | Cons | Examples | |
Bulk Polymerization |
Simple process and derives macromolecules with high purity | Hart to control exothermicity and high viscosity occurs. | -Continuous polymerization of styrene.
– Casting of methacrylate plate – Continuous polymerization of polyvinyl |
Suspension Polymerization |
Easy heat dissipation and derives macromolecules with low viscosity available as it is. | This reaction needs cleaning and dehydration. Polymer cogulation can occur, and purity of polymer is getting low due to pollution by addictive. | – Adhesives made from polyvinyl acetate
– Rubber made from polypropylene and polybutadiene. |
Solution Polymerization |
Easy heat dissipation and derives macromolecules with low viscosity available in solution. | The solvent for reaction is expensive, hard to remove solvent completely, and chain transfer reaction with solvent can occur. | Beads, pvc powder made from foamed polyethylene, polystyrene, PMMS. |
Emulsion Polymerization |
Easy heat dissipation and derives macromolecules with low viscosity available in emulsion. This is suitable for mucoadhesive polymers. | Purity of polymer is getting low due to emulsifier and other addictives | – Polyvinyl, polyvinyl acetate, polystyrene
– Resin finishing agent for SBR, NBR, concrete |